- Reaction score
- 5,636
This is only the second time I have had to crimp 6mm cable. I remember the first time a couple of years ago I had problems. Again this time the connection just pulled apart in my hands.
After looking through the forum I can see that others have had the same problem specifically with yellow crimps. 1mm and 2.5mm seem to crimp perfectly well (again seen in other threads), but with 6mm there is a problem.
The reason for this thread is because other threads point to the crimp or the crimping tool being the problem. I have a CK crimping tool which has good reviews and crimps 1mm and 2.5mm very well (I have tested these in a vice), so I believed the crimp to be the problem. I was about to buy some SWA crimps as other threads point to these being good quality. However, my red and blue crimps were bought from the same manufacturer as the yellow so it didn't really make sense that it was the crimp at fault.
I've just been in the shed crimping 6mm in a number of different ways and think I have found the problem. With red and blue crimps you have the crimp flush with the crimping tool when you crimp. I assumed it would be the same with yellow, however the crimping tool is wider for the yellow crimps meaning that when you crimp you are crimping the entire half of the crimp (perhaps even slightly over), meaning that you are crimping down on the piece of metal that sticks out in the middle of the crimp and I think this must be stopping the crimping tool from crimping properly.
The top crimp (see picture) was crimped with the yellow crimp (outer part) flush with the crimping tool and just pulled out easily. With the other two I slightly pushed the crimp into the crimping tool so that the central piece of metal would not be disturbed (you can see that the bottom 2 crimps have a bit in the middle still raised whereas the top one doesn't). I could not pull either of these out when placed in a vice.
Correct crimping is so important I thought I'd mention my little test. I tested the 2 ways each with 5 crimps and it was the same with all of them.
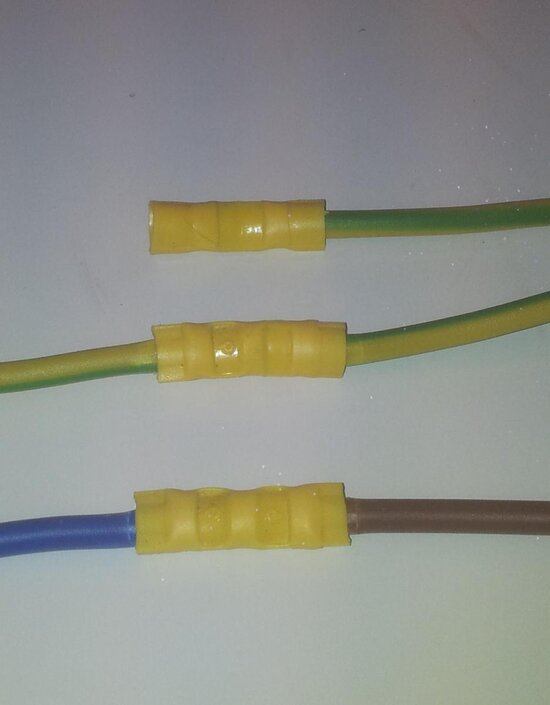
After looking through the forum I can see that others have had the same problem specifically with yellow crimps. 1mm and 2.5mm seem to crimp perfectly well (again seen in other threads), but with 6mm there is a problem.
The reason for this thread is because other threads point to the crimp or the crimping tool being the problem. I have a CK crimping tool which has good reviews and crimps 1mm and 2.5mm very well (I have tested these in a vice), so I believed the crimp to be the problem. I was about to buy some SWA crimps as other threads point to these being good quality. However, my red and blue crimps were bought from the same manufacturer as the yellow so it didn't really make sense that it was the crimp at fault.
I've just been in the shed crimping 6mm in a number of different ways and think I have found the problem. With red and blue crimps you have the crimp flush with the crimping tool when you crimp. I assumed it would be the same with yellow, however the crimping tool is wider for the yellow crimps meaning that when you crimp you are crimping the entire half of the crimp (perhaps even slightly over), meaning that you are crimping down on the piece of metal that sticks out in the middle of the crimp and I think this must be stopping the crimping tool from crimping properly.
The top crimp (see picture) was crimped with the yellow crimp (outer part) flush with the crimping tool and just pulled out easily. With the other two I slightly pushed the crimp into the crimping tool so that the central piece of metal would not be disturbed (you can see that the bottom 2 crimps have a bit in the middle still raised whereas the top one doesn't). I could not pull either of these out when placed in a vice.
Correct crimping is so important I thought I'd mention my little test. I tested the 2 ways each with 5 crimps and it was the same with all of them.
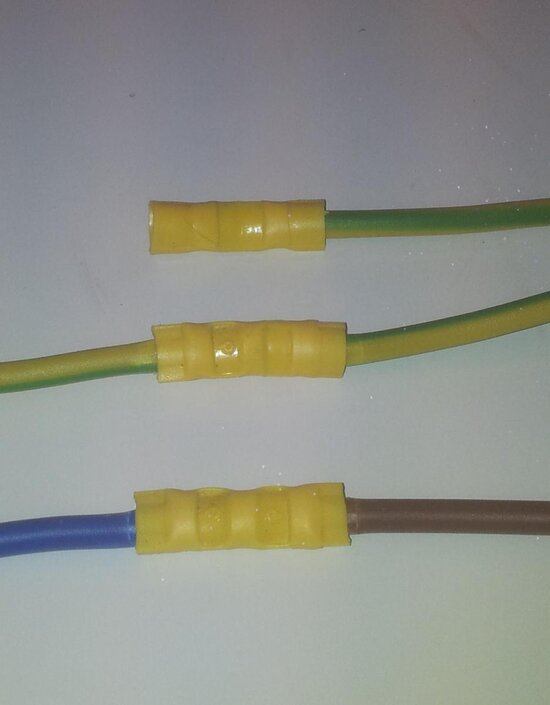
Last edited: