- Reaction score
- 1
Hi guys,
So basically I'm coming here looking for some friendly advice with the intention of eventually getting an electrician out to make sure I'm not messing anything up (I'm based near Swindon - recommendations welcome!). I just want to do as much of the prep as possible.
I've put together a wiring diagram based on what I've learnt on the web. The van is an LDV Maxus and the starter battery looks like the best thing to plug in to as the alternator is hidden away. Basically what I want to do is hook up some LED lighting and a couple of mains plugs which I can run laptop/charge camera batteries/phone etc from. The only thing I've bought so far is the 85ah leisure battery.
Based on the diagram could you kind chaps let me know if:
a) anything is going to cause a problem?
b) if anything could be improved? (I've read that the split charge relay isn't the most economical solution, but am struggling to find a replacement)
c) how I would go about working out what wires/fuses I need?
d) what size inverter should I choose? Is this even the best solution?
e) have I missed anything?
The other thing I was wondering was about the leisure battery. If using up a full charge is going to ruin it, is there some sort of mechanism I can implement to prevent this happening?
Thank you so much for your time and effort,
Scott
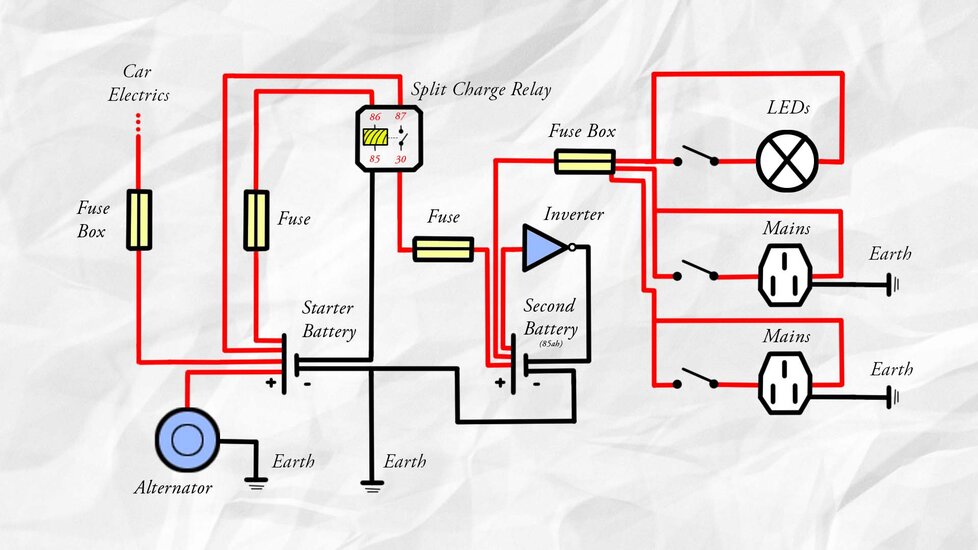
So basically I'm coming here looking for some friendly advice with the intention of eventually getting an electrician out to make sure I'm not messing anything up (I'm based near Swindon - recommendations welcome!). I just want to do as much of the prep as possible.
I've put together a wiring diagram based on what I've learnt on the web. The van is an LDV Maxus and the starter battery looks like the best thing to plug in to as the alternator is hidden away. Basically what I want to do is hook up some LED lighting and a couple of mains plugs which I can run laptop/charge camera batteries/phone etc from. The only thing I've bought so far is the 85ah leisure battery.
Based on the diagram could you kind chaps let me know if:
a) anything is going to cause a problem?
b) if anything could be improved? (I've read that the split charge relay isn't the most economical solution, but am struggling to find a replacement)
c) how I would go about working out what wires/fuses I need?
d) what size inverter should I choose? Is this even the best solution?
e) have I missed anything?
The other thing I was wondering was about the leisure battery. If using up a full charge is going to ruin it, is there some sort of mechanism I can implement to prevent this happening?
Thank you so much for your time and effort,
Scott
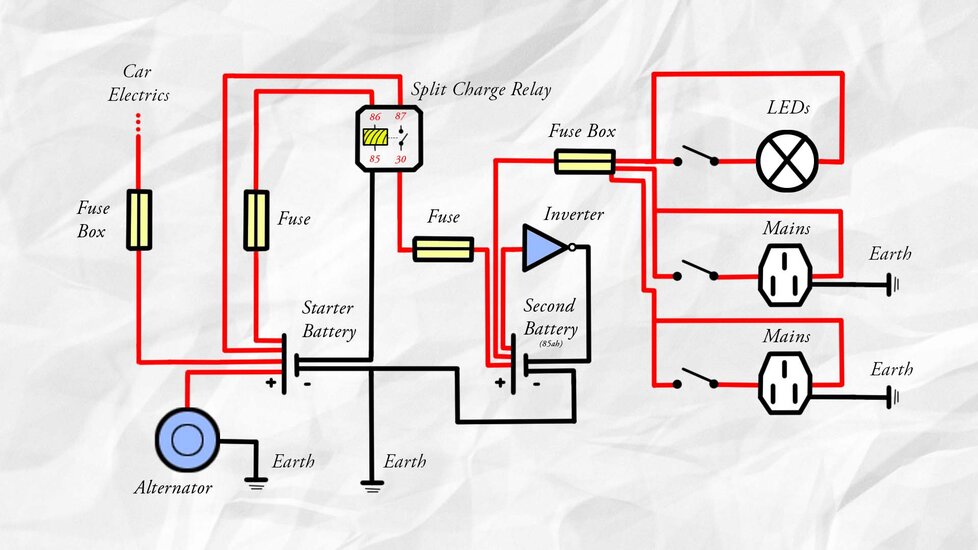