I thought my old alternator was toast (after all, it was 15 years old), but a brand new one is doing exactly the same thing: the belt is snug (and only a month old), but my system is barely charging, or not charging at all, but the belt is squealing and heating up the pulley at moderate RPM, as if it's really working hard...and leaving a steady accumulation of belt-powder around the general vicinity. I replaced the old belt recently because it had become too worn to put tension on it within the confines of the adjustment. My voltage never gets above 12.8-ish. Brand new battery - a few days old - still starts fine, but is not getting charged much if at all. Ign lite either dims, or stays on full brightness, regardless of RPM. There's no visible drop in headlight brightness when the engine is switched off.
But from the squeal and heating of the pulley, it's like the alternator is being taxed heavily, the charge being dissipated in some invisible load-bank. I've retensioned the belt a number of times, and each time am greeted with more squealing. And no, it's not OVERtightened, either. So where's all that energy GOING?
Since I can't think what else to do, I'd like to make temporary bypass connection/s to the new alternator, now in the car, so as not to assume anything about my existing wiring. I've always run the previous alt (this one's a Lucas 45A replacement for 16ACR and 17ACR) on two wires only, and this model has only two connections (see photo)
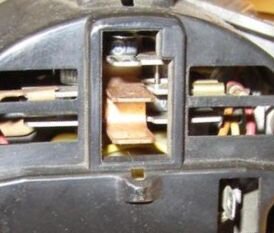
so it should be simple to test in situ. Can someone please confirm, then, that to test the basic functions, I might wire/test as follows:
1) run either fat (wide quick-disconnect lugs) brown lead to +12VDC
2) run small brown/yel lead, connected through an auto test-light, to +12VDC
Testing:
a) with power in place as above, and engine not running, test light should be ON.
b) with engine running - and perhaps RPM revved up and then kept up a bit above idle - test light should dim and go out, and voltage on fat brown lead should be somewhere in the range of, say, 13.5-14.5V
c) With belt snug (about 1/2" up/down play with pressure from thumb on belt), no squealing should be heard.
What else could be the problem?
But from the squeal and heating of the pulley, it's like the alternator is being taxed heavily, the charge being dissipated in some invisible load-bank. I've retensioned the belt a number of times, and each time am greeted with more squealing. And no, it's not OVERtightened, either. So where's all that energy GOING?
Since I can't think what else to do, I'd like to make temporary bypass connection/s to the new alternator, now in the car, so as not to assume anything about my existing wiring. I've always run the previous alt (this one's a Lucas 45A replacement for 16ACR and 17ACR) on two wires only, and this model has only two connections (see photo)
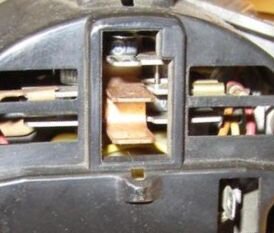
so it should be simple to test in situ. Can someone please confirm, then, that to test the basic functions, I might wire/test as follows:
1) run either fat (wide quick-disconnect lugs) brown lead to +12VDC
2) run small brown/yel lead, connected through an auto test-light, to +12VDC
Testing:
a) with power in place as above, and engine not running, test light should be ON.
b) with engine running - and perhaps RPM revved up and then kept up a bit above idle - test light should dim and go out, and voltage on fat brown lead should be somewhere in the range of, say, 13.5-14.5V
c) With belt snug (about 1/2" up/down play with pressure from thumb on belt), no squealing should be heard.
What else could be the problem?